Despite guidelines against sub-standard materials in block making, Lagos roadside operators violate Nigeria’s Cement Grade Policy meant to curb incessant building collapse, writes SAMUEL DIALA
At Pipeline Bus Stop on the 20-kilometre Idimu Road, Egbeda, Alimosho Local Government Area of Lagos State, is a roadside block-moulding ‘industry’. The business is owned by Mr Akeem Adekunle (not real name), a 62-year-old man popularly called Baba Block. He has run the business in the same venue for about 16 years since he lost his security job in a textile company in 2002, and after two years of apprenticeship.
Adekunle’s enterprise represents similar roadside block-moulding ‘industries’ that dot Lagos suburbs – Ikorodu, Ajegunle, Agege, Ikotun, Okokomaiko and many other areas. The three major raw materials Adekunle needs – cement, sand and water, are within the vicinity. There is cement seller opposite his ‘industry’ near a car wash where he fetches water when the drainage channels are dry. Adekunle hardly buys sand during rainy season because the floods gather huge sands in the shallow roadside drainages.
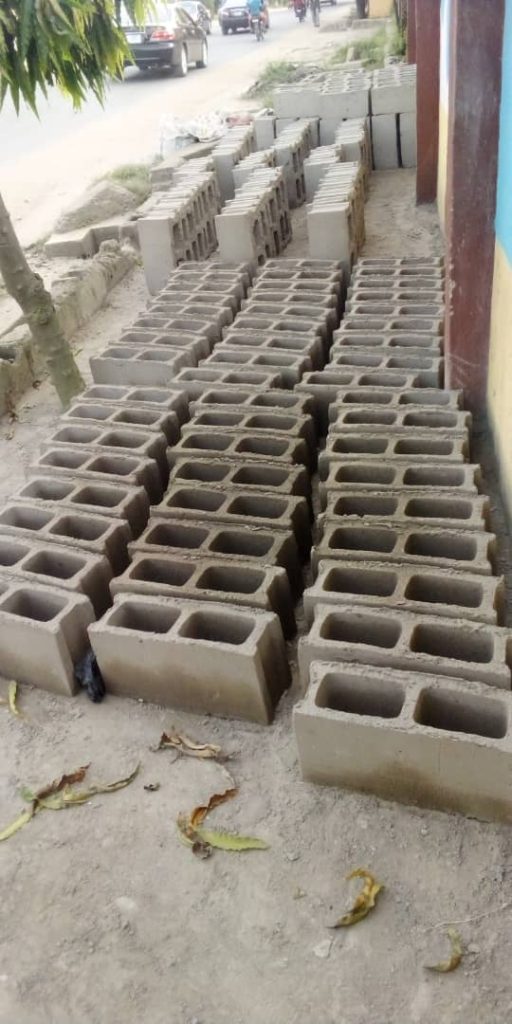
Baba Block insists on cash payment because, according to him, he had been defrauded through a fake bank credit alert. He would not disclose his turnover for fear of attracting Lagos revenue officials. “I can’t say how much I make because I don’t want to be reported to Lagos tax officials. But I make a little margin after my expenses”. However, he parts with N500 every week to the “Omoniles” (land owners) who come on Saturdays to collect the “Baale money” (gift for local chief). He also pays “some tax” to local government and security levy where he packs his tools.
He documsents his transactions in his own way. “Documentation is no problem”, said Adekunle. “I have a book where I record what I spend and receive every day. It is my private record; I don’t show it to anybody except my wife at home who keeps the money before I take it to the bank”, he told NextMoney during an interview. He said he sells between 300 and 800 blocks a week “depending on market” but engages in no marketing or canvasing. “I am in a strategic location; people know me. I have been here for about 16 years now.” It is obvious Baba Block enjoys conducive operating environment; but the business runs in violation of government’s Cement Grade Policy.
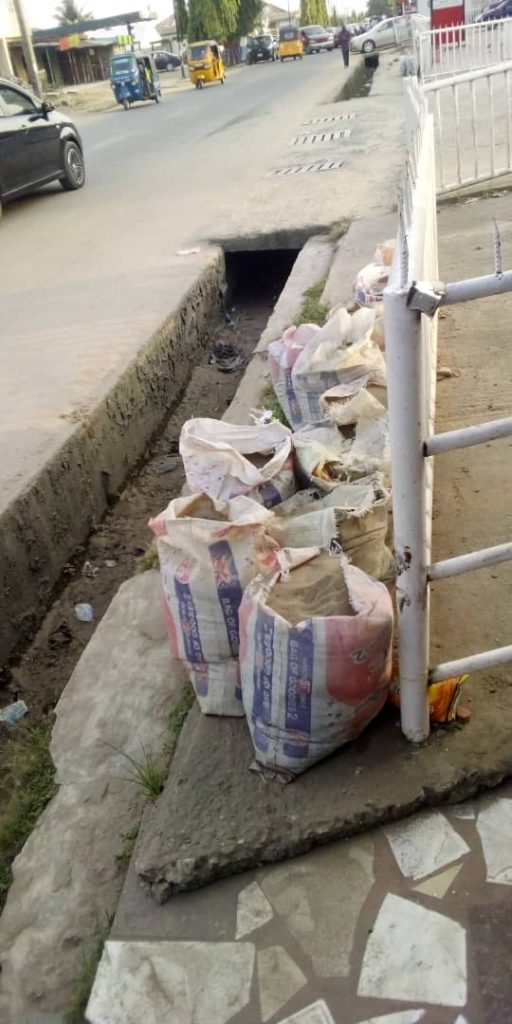
Wither Cement Grade Policy
Worried by incessant building collapse across the country, the Standards Organisation of Nigeria (SON) introduced the Cement Grade Policy in June 2014 to curb the menace. The agency had revealed that only five per cent of blocks sold in Nigeria were mould to specifications of the required standard, and that the anomaly was the major cause of building collapse in the country. It therefore set out to regulate the quality of cement used in block-making and in other aspects of construction.
“We did a national survey on the quality of concrete blocks in Nigeria, especially the low bearing ones and found out that only five per cent of the blocks are mould to specifications of standard of the NIS587:2007. That necessitated what we are doing here today. We believe it is important that anything that is remotely or directly contributing to building collapse in Nigeria should be addressed,” Dr. Joseph Odumodu, former Director-General, SON, said at a national stakeholders forum on blocks and allied products held in 2015 in Lagos, with the theme: ‘Safeguarding lives through compliance with standards’.
The controversy generated an uproar among cement manufacturers, dealers, builders, engineering groups, regulatory bodies, the organised labour and block-moulders. Based on a petition by some stakeholders, the House of Representatives constituted an 8-member Ad-hoc Committee to investigate the matter, with the following Terms of Reference:
(i)To determine the role of cement in the incessant building collapse in the country;
(ii)To investigate and determine the quality and grades of cement produced, packaged or imported into Nigeria;
(iii)Recommend ways of eliminating substandard cement in Nigeria and/or standardizing cement quality in Nigeria.
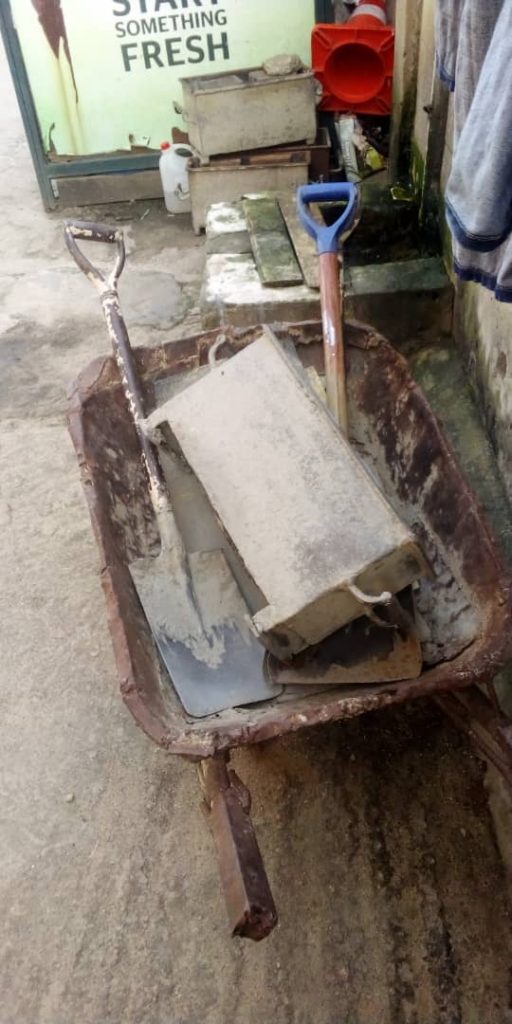
Referred to as “Committee on the Composition and Pigmentation of Cement in Nigeria”, the team of lawmakers, headed by Hon. Yakubu Dogara as chairman, held Public Investigative Hearing during which 25 invited stakeholders – Government ministries and agencies, cement manufacturers, professional groups and Non-governmental organisations – made appearance on appointed dates.
NextMoney cited the Committee’s 32-page report coded “Resolution No. HR.27/2014 of June 2014” presented to the House at plenary. Some of the stakeholders had argued that “there was no scientific proof of the contribution of cements to incidences of collapsed buildings in the country”. This group rather attributed the unhealthy development to “non-adherence to professional ethics, wrong combination of materials, poor supervision, corruption” among the causes.
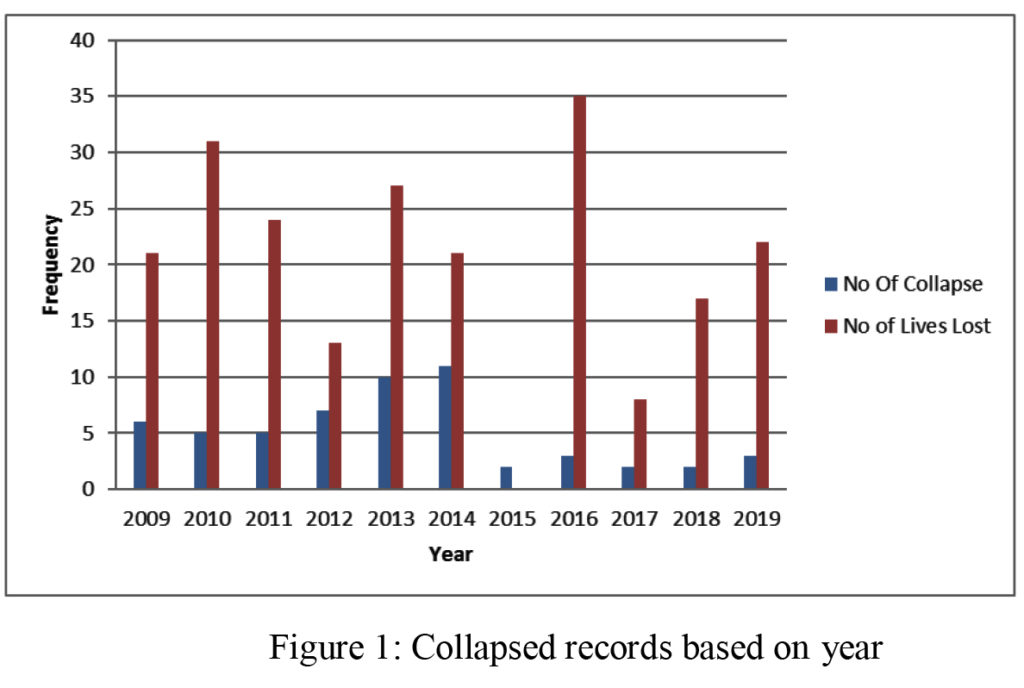
However, another group attributed the incessant building collapse to sub-standard blocks made with low-grade cement. According to this group, three categories of cement are in use in Nigeria: the 32.5 grade, 45.2 grade and the 52.5 grade. The group expressed concern over the “misapplication of the 32.5 grade cement meant for plastering not for block-moulding”. They reiterated that the 32.5 grade should be used strictly for plastering; while 45.2 grade is used for block-moulding and 52.5 grade for high-level structures.
Notwithstanding the contending views during the public hearing, SON went ahead to ‘enact’ the Cement Grade Policy. This was published in national newspapers by way of advertorials, stipulating guidelines for deployment of the three cement grades in building and other construction works. The House Committee, expectedly, backed the Cement Grade Policy, noting that “the 32.5 grade is the most susceptible to manipulation.” It adopted the Policy which, among other things, banned activities of roadside block-makers and the use of manual moulding.
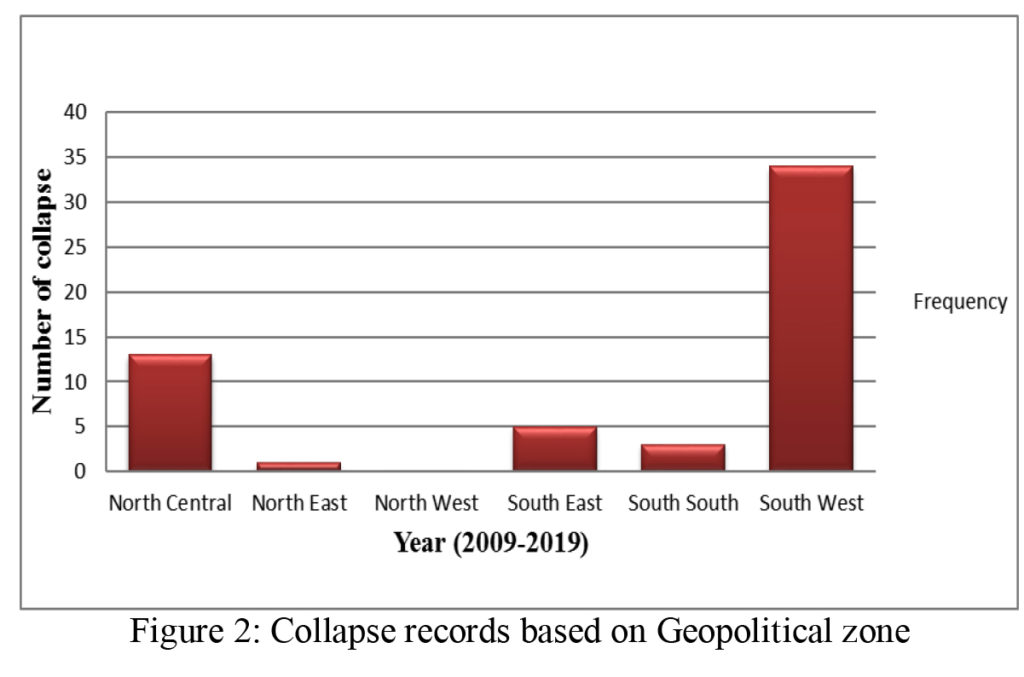
Specifically, the Cement Grade Policy of 2014 stated that 52.5 grade cement must be used for bridges, 42.5 grade cement for casting of columns, beams, slabs and for moulding blocks, while 32.5 grade cement can only be used for plastering. SON and the National Association of Block Moulders of Nigeria (NABMN) subsequently agreed that only 24 blocks should be produced from a 50kg bag of cement and not 42 as was being done. They also arrived at a particular mix in ratio of other additives which would produce 24 blocks from a 50kg bag of cement, stating that the 42 blocks produced from the same quantity of cement were substandard.
Compliance in breach
Findings show that roadside block-making remains a thriving business in Lagos. The operators still use the 32.5 cement grade for moulding. Adekunle told NextMoney that he produces about 40 blocks from a 50kg bag of 32.5 cement grade using manual system. A structural engineer, Tim Akinsola, said the roadside block-moulders are flouting the rule. “The sand quality is poor; there is inappropriate mix of the coarse aggregate; even the drainage channel water is not suitable. It is sad that these people have illegally remained in business despite the ban on their activities”, Akinsola said.
NextMoney findings further revealed that government contractors are among the major patronizers of roadside block-moulders. Builders use the roadside blocks on top of the ‘stronger ones’ at a level from foundation. The newly reconstructed Ile-Epo food market in Oke-Odo LCDA on the Lagos-Abeokuta Expressway, Lagos, was executed with much of roadside blocks, according to a builder who would not want his name published to avoid being sanctioned by the state government. “People use these blocks for shops, culverts, security houses and other ‘small, small’ buildings because they are cheaper,” Adekunle said.
A professor of building at the University of Lagos, Godwin Idoro, in a paper presented at the Building Collapse Prevention Guild’s workshop for block moulders in Lagos, called for a ban on the use of manually produced blocks for building construction to check the menace of structural failures and collapse. Idoro said, “The use of non-mechanical method of production should be stopped; it is time for all stakeholders to discourage the use of manually produced blocks. There is a need to encourage fabrication and production of better locally produced block-moulding machines.”.
The incumbent Director-General of SON, Osita Aboloma, said the Organisation has resolved to deploy the use of block testing machines to check production of substandard blocks in the country. According to him, the agency is strengthening its collaboration with block moulders in the country by rolling out block testing machines in large number. He said this would give block moulders the opportunity to test their blocks while also complying to standards because the Cement Grade Policy is still in place.
Adekunle’s roadside block-moulding ‘industry’ points to the prevalence of the banned business across the country. NextMoney confirmed through the phone that micro-block businesses operate freely in Nbawsi, Isiala Ngwa LGA of Abia State; Umuokanne, Ohaji/Egbema LGA of Imo State; Gboko, Benue State; Offa, Kwara State and the suburbs/satellite towns of Abuja FCT.
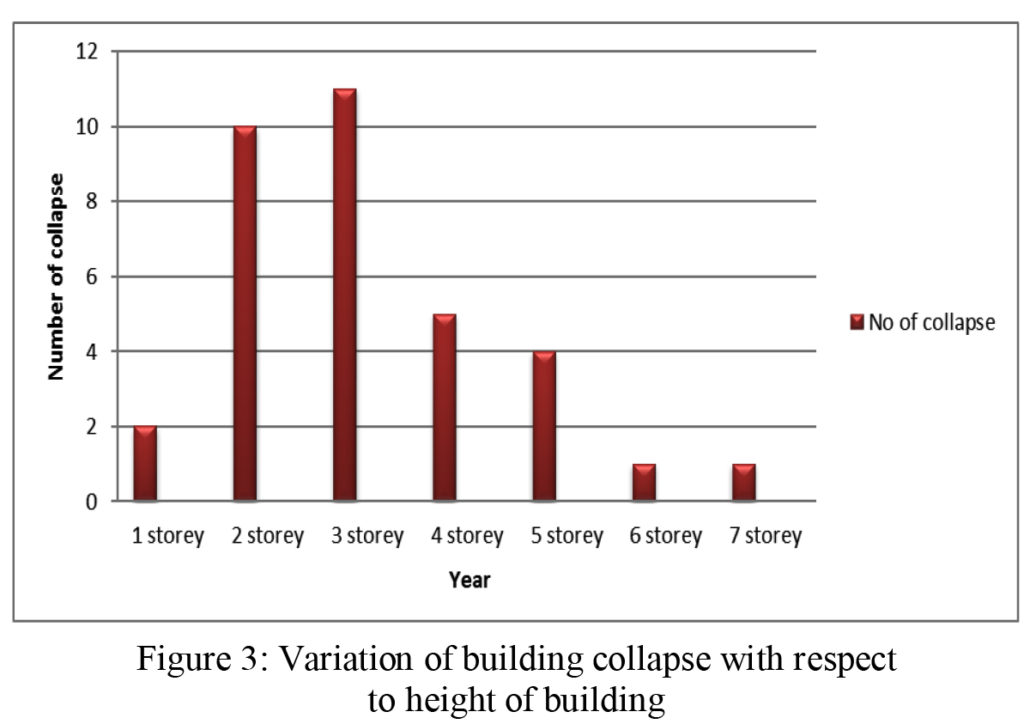
Block-makers in perspective
Nigeria’s small business sector is divided into Micro, Small and Medium Enterprises (MSME). Micro group are enterprises of between 1 and 9 employees and capital base of below N5 million. Small and Medium Enterprises group consist of enterprises of between 10 and 49 employees with capital base of less than N50 million; and employee size of between 50 and 249 with capital base of above N50 million respectively.
The Ministry of Industry, Trade and Investment says Nigeria has over 37.07 million MSMEs and they account for more than 84 per cent of total jobs in the country. The ministry also revealed that the MSME enterprises in Nigeria also account for about 48.5 per cent of the gross domestic product, GDP, as well as about 7.27 per cent of goods and services exported out of the country. According to Small and Medium Enterprise Development Agency of Nigeria (SEMEDAN), micro enterprises account for the bulk with 36.994,578 (about 99.8 per cent), while small enterprises took 68,168 and medium enterprises 4,670. Roadside block makers belong to the Micro enterprise group.
NextMoney findings showed that roadside block-makers do not belong to the National Association of Block Moulders of Nigeria (NABMN) which are recognized by SON and most of which fall into the higher categories of SMEs. They use mechanized facilities for their products. Commenting on the incessant monitoring by SON officials, Alhaji Rasheed Adewale, President, NABMN, said their members, unlike the roadside block-makers, comply with the Cement Grade Policy even at a great cost to their members.
Condemning the activities of the roadside moulders, Adewale noted that SON, as a government agency, should be obeyed to check the incessant building collapse across the country. “Nobody has a right to challenge standards set by SON because the organisation is the arm of government responsible for enforcing standards. What concerns us is the 42.5 grade approved by SON in accordance with Nigeria Industrial Standards. In the past every grade of cement was used to produce blocks which is the cause of the national embarrassment building collapse causes. SON saw the need to provide standards in the block industry. Let everybody in the industry comply with it,” he said.
Conclusion
The Cement Grade Policy appears to be ‘standing’ in limbo. NextMoneyfound that the initial fierce anger of SON against micro roadside block-moulders seems to have lost steam. Economic realities embedded in rising unemployment, high cost of living and other prevailing challenges combined to put the Cement Grade Policy in the cooler. It appears to be observed more in the breach by the micro-block producers.
Figures obtained from the Building Collapse Prevention Guild, an advocacy group of built environment professionals, showed that Nigeria recorded about 60 building collapses in four years (2016-2019). Some stakeholders and experts maintain that the 32.5 cement grade is not responsible for the prevalence of building collapse. But SON thinks otherwise, insisting that the Cement Grade Policy stands:
“The menace of building collapse is very worrying. It is not rocket science to know that the actual people we will work with to address this menace is the block moulders at the grassroots. We are in the process of deploying about 55 locally made block testing machines. This is part of our efforts to increase the patronage of made-in-Nigeria goods as against the imported ones. This will go a long way to help your association get the right and quality blocks,” Aboloma said at a stakeholders meeting with block-moulders association in Lagos last year.
The Cement Grade Policy notwithstanding, micro block business operators are still in existence. “No government policy can stop us from doing our legitimate business. We are in business to meet the needs of small customers and to earn a living. We are self-employed; and we create jobs too. Let the small producers and consumers be; let the big producers and consumers be. We are not the cause of building collapse because 32.5 cement grade has been in existence in Nigeria and used in constructing buildings that still stand today,” Adekunle said.
This investigation was supported by the US Embassy via the ATUPA Fellowship by Civic Hive